Galvalume Roofing Sheet
Product Introduction of Galvalume Roofing Sheet
Galvalume roofing sheet is popular in commercial, residential, agricultural, and industrial applications. It is covered with a coating of aluminum-zinc alloy, which gives it excellent corrosion and heat resistance. Due to its superior performance, it is ideal for homeowners, contractors, architects and investors. Shandong Baomai Steel manufactures a wide range of metal roofing products in different materials, including GI, GL, PPGI and PPGL in various sizes and designs to meet your requirements. Feel free to contact us for more details!
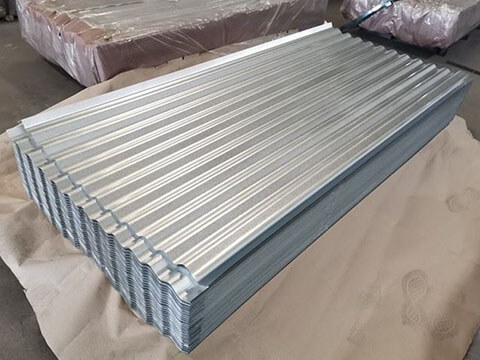
Specifications of Galvalume Roofing Sheet
Item | Galvalume Roofing Sheet |
Coating | Al-Zn alloy |
Thickness | 0.13-1.2 mm |
Width | 600-1250 mm |
Length | As per your requirements |
Surface Treatment | Coated or bare galvalume |
Packaging | Standard export packaging |
Application of Galvalume Roofing Sheet
Galvanized steel sheets are used for residential and commercial roof installation projects.
1. Commercial buildings – hospitals, schools, stores, government buildings, etc.
2. Residential projects – private homes, apartments, temporary housing, garages, etc.
3. Industrial applications – warehouses, factories, etc.
4. Agricultural applications – barns, storage rooms, greenhouses, etc.
What is the difference between galvanized roofing and galvalume roofing?
When completing a project with corrugated sheeting, should you choose galvanized metal roofing or galvalume metal roofing?
The answer lies in the difference between the two. Traditional galvanized metal roofing is a corrugated carbon steel sheet with a galvanized coating. This coating is formed by dipping the straight sheet into hot, molten zinc. The zinc ions combine with the iron molecules in the steel to form a shiny, rust-resistant coating on its surface. This process is known as galvanizing.
After the coating hardens, the sheet is placed in a cold forming corrugation process that bends the sheet into a parallel linear pattern. These “corrugations” give the sheets greater strength and stability when installed as a roof.
As the coating dries, patches of aluminum and zinc molecules coalesce into a pattern on the surface of the sheet. The aluminum zone provides corrosion resistance, while the zinc provides galvanizing protection. A small amount of silicon helps the coating adhere to the underlying metal, even when it is cut or rolled into a corrugated pattern.
So, which is better for roofing? Each type has advantages and disadvantages.
Galvalume’s extra corrosion resistance means scratched, bent, or cut edges won’t rust as quickly, and it’s also a better choice in rainy climates and salty air.
The paint does not adhere well to Galvalume, so the aesthetic appeal may not be as good. In addition, Galvalume costs more than galvanized metal roofing – but the fact that Galvalume metal roofing will last twice as long as galvanized roofing of the same thickness can make up the difference. For these reasons, Galvalume metal roofs are more popular.
Typically, galvanized sheet metal roofing is used primarily for agricultural buildings where rusting is not as much of a problem and costs must be kept low. Galvanized metal roofing may also be used by architects looking for a traditional, rusty look in new construction.
What Is Galvalume Metal Roofing?
Galvalume metal roofing sheets are coated with a blend of 55% aluminum, 43.4% zinc, and 1.6% silicone to protect the base steel from corrosion and rusting. Therefore, it is suitable for most applications, including in extreme environments. In addition, galvanized steel roofing offers a smaller, smoother patina, which results in a more uniform surface. Let’s review the differences between galvanized roofing panels and aluminized zinc roofing panels.
Galvanized Roofing Panels VS Galvanized Roofing Panels
These two types of metal roofing panels are steel substrates that are coated with different coatings and then molded into the corrugated design of the roof. Their characteristics are very different.
Galvanized panels are coated with an aluminum and zinc alloy (55% aluminum, 43.4% zinc, 1.6% silicon), while galvanized steel is covered with a zinc coating. Compared to galvanized sheets, aluminum has a natural ability to resist corrosion and better protects the steel core from corrosion. This means that galvanized sheet has better corrosion and heat resistance than galvanized materials.
FAQ
The corrosion resistance of stainless steel coils decreases as the carbon content increases. Therefore, the carbon content of most stainless steels is low, up to 1.2%, and some steels have a low ωC (carbon content) of even less than 0.03% (such as 00Cr12). The main alloying element in stainless steel coil is Cr (chromium). Only when the Cr content reaches a certain value, the steel has corrosion resistance. Therefore, the goods Cr (chromium) content of at least 10.5%. Stainless steel coil also contains Ni, Ti, Mn, N, Nb, Mo, Si, Cu and other elements.
Most of the requirements for use are to maintain the original appearance of the building for a long time. In determining which type of goods to choose, the main considerations are the required aesthetic standards, the corrosiveness of the local atmosphere and the cleaning system to be used. However, other applications are increasingly seeking structural integrity or impermeability. Examples include roofs and sidewalls of industrial buildings. In these applications, construction cost to the owner may be more important than aesthetics, and the surface may not be very clean. The use of 304 stainless steel coils in dry interior environments is quite effective.
Weldability. Different product uses have different requirements for weldability. A class of tableware generally does not require weldability, even including some cookware companies. However, most products require raw materials with good weldability, such as second-class tableware, insulation cups, steel pipes, water heaters, water dispensers, etc.
Corrosion resistance. Most stainless steel coil products require good corrosion resistance, such as Class I or Class II tableware, kitchen utensils, water heaters, water dispensers, etc.
Polishing performance. In today’s society, stainless steel coil products in the production process are generally polished, only a few products such as water heaters, drinking fountains, etc. do not need to be polished. Therefore, this requires raw materials with good polishing performance.
1. The need for pre-treatment
Pretreatment is an important treatment step before the surface of stainless steel coil parts enter surface treatment (including pickling, chemical polishing and electrochemical polishing, electroplating, passivation, black coating, coloring, chemical treatment, etc.). During the forming process of goods parts, the surface may adhere to oil stains, burrs, rough surfaces and oxides. Therefore, before surface treatment, oil stains, burrs, uneven surfaces and oxides must be removed in order to obtain subsequent satisfactory results through processing.
2. Treatment of removed dirt
Stainless steel coil surface pretreatment in the need to remove the dirt can be divided into two categories: organic and inorganic substances.
(1) organic dirt. Including mineral oil (such as diesel, oil, paraffin, gypsum, etc.) and animal oil, vegetable oil (such as soybean oil, camellia oil, rapeseed oil, lard, butter, etc.). These oils are mainly from the stainless steel coil zero cattle processing process used in the lubricant. , cutting oil, quenching oil, polishing paste and polishing paste, and fingerprints.
(2) Inorganic dirt. Including dirt, dust particles, oxides and other contaminants generated during the heat treatment process.
3. Pretreatment steps for stainless steel coil parts
(1) The surface is mechanically leveled. Eliminate the roughness of the stainless steel coil surface, through mechanical polishing and grinding to achieve a surface finish.
(2) Degreasing. Remove the surface oil and dirt.
(3) Acid washing. Remove the oxides on the surface.
(4) Weak corrosion. Activates the surface to be treated, removes the surface passivation film, and exposes the metal crystal structure.
Stainless steel is a high-alloy steel, with a large resistance to rolling deformation. In order to carry out high-efficiency and high-precision rolling, rigid rolling mills should be used, generally multi-roller cold rolling mill.
Special welding process is also a feature of cold-rolled stainless steel coil production.
In the production process of cold rolled stainless steel coil, the raw material (hot rolled coil) should be annealed, intermediate annealing should be carried out in the cold rolling process, and the final product should be annealed, so annealing is an important part of the production.
Cold-rolled stainless steel is a high-grade steel products, there are strict requirements for surface quality. Not only are metallurgical defects caused by the previous process not allowed, but also obvious defects caused by the cold rolling process.
Hot Products
Keywords:
- Galvalume Coil
- Roofing Sheet
Share to: