Galvalume Steel Coil
Product Introduction of Galvalume Steel Coil
Aluminized zinc steel coil is made of cold rolled steel sheet as the base material and is made of 55% aluminum, 43.4% zinc and 1.6% silicon cured at 600°C. It combines the physical protection and high durability of aluminum with the electrochemical protection of zinc. It is also known as aluminum-zinc alloy steel coil.
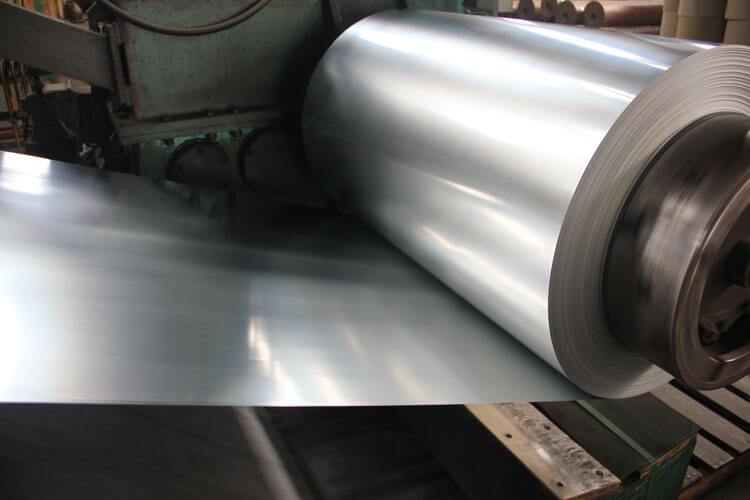
Specification of Galvalume Steel Coil
Product name | Galvalume Steel Sheet in Coil |
Material | CGCC, DX51D,Q195,Q235 |
Grade | SGCC,DX51D+Z |
Alu-Zinc Coating | 20-120g/m2 |
Thickness | 0.13-0.7 mm |
Width | 600-1250 mm |
Coil ID | 508/610mm |
Coil weight | 3-8tons |
Surface Structure | Mini/Big Spangle |
Surface Treatment | Anti-Finger printing ,Chromated, oiled/ non-oiled |
Package | standard export package (Detailed picture is as follows) |
Hardness | soft (normal), hard, full hard(G300-G550) |
HS code | 721049 |
Country of origin | China |
Business type | Supplier and manufacturer |
Brand name | BAOWU |
Application of Galvalume Steel Coil
Unique protective properties and affordability make Lapham-Hickey’s galvanized steel coils and sheets ideal for a wide range of applications, including but not limited to
- Residential and commercial exterior construction products
- Roofing
- Wall panels
- Cabinets
- Air conditioning and heating equipment
- Electrical boxes
- Farm equipment and machinery
- Furnace components
- Guide rails
- Home appliances
The difference between galvanized and electro-galvanized
The main difference lies in their coating. In the case of galvanized sheet, a layer of zinc material is distributed evenly over the surface of the galvanized sheet and provides active protection to the base metal; in other words, zinc serves as a substitute for corrosion protection of the base metal until it is torn off.
In contrast, the surface of the galvanized sheet is a coating consisting of 55% aluminum, 43.5% zinc, and some other elements, which look like a honeycomb structure under a microscope. In this case, although the coating of the galvanized sheet also plays its protective role as an anode plate, this protective effect decreases dramatically because the zinc content decreases and because the zinc is not easily electrolyzed when it is encased in aluminum.
Therefore, once the galvanized sheet is cut, the cut will generally lose its protective effect and will rust soon. Therefore, we should try to cut as little as possible, and once cut, use rust-proof paint or zinc-rich paint to protect the cut and prolong its life.
Advantages of galvanized steel
Can handle the heat. Performs well above 300°C.
Prevents corrosion. The aluminum layer provides protection for the interior of the steel.
Easy to paint. Galvanized steel provides perfect adhesion and gives you an attractive paint finish.
FAQ
The corrosion resistance of stainless steel coils decreases as the carbon content increases. Therefore, the carbon content of most stainless steels is low, up to 1.2%, and some steels have a low ωC (carbon content) of even less than 0.03% (such as 00Cr12). The main alloying element in stainless steel coil is Cr (chromium). Only when the Cr content reaches a certain value, the steel has corrosion resistance. Therefore, the goods Cr (chromium) content of at least 10.5%. Stainless steel coil also contains Ni, Ti, Mn, N, Nb, Mo, Si, Cu and other elements.
Most of the requirements for use are to maintain the original appearance of the building for a long time. In determining which type of goods to choose, the main considerations are the required aesthetic standards, the corrosiveness of the local atmosphere and the cleaning system to be used. However, other applications are increasingly seeking structural integrity or impermeability. Examples include roofs and sidewalls of industrial buildings. In these applications, construction cost to the owner may be more important than aesthetics, and the surface may not be very clean. The use of 304 stainless steel coils in dry interior environments is quite effective.
Weldability. Different product uses have different requirements for weldability. A class of tableware generally does not require weldability, even including some cookware companies. However, most products require raw materials with good weldability, such as second-class tableware, insulation cups, steel pipes, water heaters, water dispensers, etc.
Corrosion resistance. Most stainless steel coil products require good corrosion resistance, such as Class I or Class II tableware, kitchen utensils, water heaters, water dispensers, etc.
Polishing performance. In today’s society, stainless steel coil products in the production process are generally polished, only a few products such as water heaters, drinking fountains, etc. do not need to be polished. Therefore, this requires raw materials with good polishing performance.
1. The need for pre-treatment
Pretreatment is an important treatment step before the surface of stainless steel coil parts enter surface treatment (including pickling, chemical polishing and electrochemical polishing, electroplating, passivation, black coating, coloring, chemical treatment, etc.). During the forming process of goods parts, the surface may adhere to oil stains, burrs, rough surfaces and oxides. Therefore, before surface treatment, oil stains, burrs, uneven surfaces and oxides must be removed in order to obtain subsequent satisfactory results through processing.
2. Treatment of removed dirt
Stainless steel coil surface pretreatment in the need to remove the dirt can be divided into two categories: organic and inorganic substances.
(1) organic dirt. Including mineral oil (such as diesel, oil, paraffin, gypsum, etc.) and animal oil, vegetable oil (such as soybean oil, camellia oil, rapeseed oil, lard, butter, etc.). These oils are mainly from the stainless steel coil zero cattle processing process used in the lubricant. , cutting oil, quenching oil, polishing paste and polishing paste, and fingerprints.
(2) Inorganic dirt. Including dirt, dust particles, oxides and other contaminants generated during the heat treatment process.
3. Pretreatment steps for stainless steel coil parts
(1) The surface is mechanically leveled. Eliminate the roughness of the stainless steel coil surface, through mechanical polishing and grinding to achieve a surface finish.
(2) Degreasing. Remove the surface oil and dirt.
(3) Acid washing. Remove the oxides on the surface.
(4) Weak corrosion. Activates the surface to be treated, removes the surface passivation film, and exposes the metal crystal structure.
Stainless steel is a high-alloy steel, with a large resistance to rolling deformation. In order to carry out high-efficiency and high-precision rolling, rigid rolling mills should be used, generally multi-roller cold rolling mill.
Special welding process is also a feature of cold-rolled stainless steel coil production.
In the production process of cold rolled stainless steel coil, the raw material (hot rolled coil) should be annealed, intermediate annealing should be carried out in the cold rolling process, and the final product should be annealed, so annealing is an important part of the production.
Cold-rolled stainless steel is a high-grade steel products, there are strict requirements for surface quality. Not only are metallurgical defects caused by the previous process not allowed, but also obvious defects caused by the cold rolling process.